“From past to future, the AR15 BCG continues to evolve.”
History of the AR15 BCG
The AR15 Bolt Carrier Group (BCG) has undergone significant evolution since its inception in the 1950s. Originally designed by Eugene Stoner for the Armalite AR-15 rifle, the BCG has seen numerous improvements and modifications over the years to enhance its performance and reliability.
One of the key historical developments in the evolution of the AR15 BCG was the introduction of the forward assist feature. This addition, which first appeared on the M16A1 rifle in the 1960s, allowed soldiers to manually push the bolt into battery in the event of a malfunction. This feature proved to be invaluable in combat situations, where reliability and quick action are essential.
Another important milestone in the history of the AR15 BCG was the introduction of the chrome-lined BCG. This innovation, which first appeared in the 1970s, helped to increase the durability and longevity of the BCG by reducing wear and corrosion. Chrome lining also made the BCG easier to clean and maintain, further enhancing its reliability in the field.
In the 1980s, the introduction of the M16A2 rifle brought about further improvements to the AR15 BCG. One of the most notable changes was the addition of a heavier buffer to reduce recoil and improve accuracy. This modification helped to make the AR15 BCG more user-friendly and comfortable to shoot, especially for those with less experience or training.
As the AR15 platform continued to evolve, so too did the BCG. In the 1990s, the introduction of the M4 carbine brought about the development of the M4 profile BCG. This design featured a shorter and lighter bolt carrier, which helped to reduce the overall weight of the rifle and improve its handling characteristics. The M4 profile BCG quickly became popular among civilian shooters and law enforcement agencies for its compact size and enhanced performance.
In recent years, advancements in materials and manufacturing techniques have further improved the AR15 BCG. The use of advanced alloys and coatings has helped to increase the strength and durability of the BCG, while also reducing friction and wear. These developments have made the AR15 BCG more reliable and efficient than ever before, ensuring that it remains a popular choice among shooters of all skill levels.
Looking ahead, the future of the AR15 BCG is bright. Continued advancements in technology and design are likely to further enhance the performance and reliability of the BCG, making it an even more versatile and effective component of the AR15 platform. Whether for military, law enforcement, or civilian use, the AR15 BCG will continue to play a vital role in the evolution of the modern rifle.
In conclusion, the history of the AR15 BCG is a testament to the ingenuity and innovation of firearms designers and engineers. From its humble beginnings in the 1950s to its current state of advanced technology, the AR15 BCG has come a long way in terms of performance and reliability. With continued advancements on the horizon, the future of the AR15 BCG looks brighter than ever.
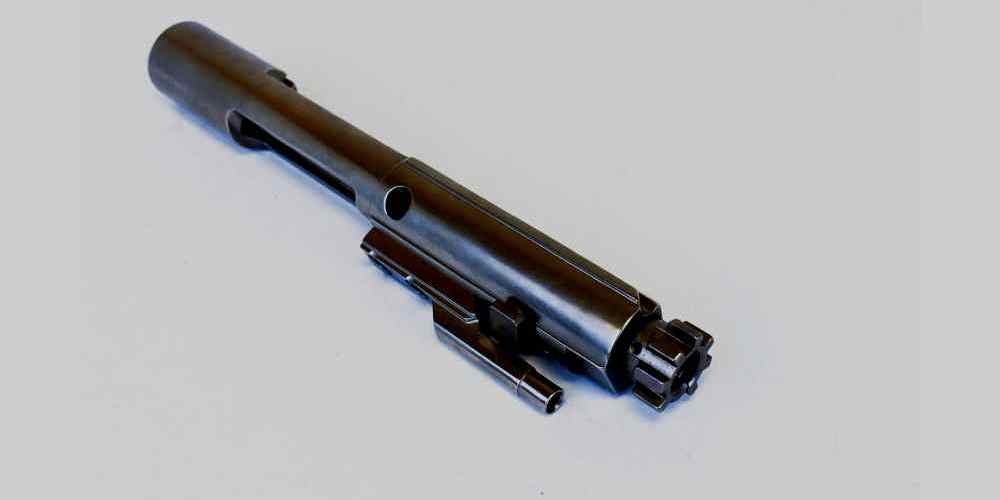
Evolution of Materials Used in AR15 BCG
The AR15 Bolt Carrier Group (BCG) has undergone significant evolution over the years, with advancements in materials playing a key role in improving its performance and durability. In this article, we will explore the historical developments of the AR15 BCG and discuss the future trends in materials used in its construction.
When the AR15 was first introduced in the 1960s, the BCG was typically made from steel. While steel is a strong and durable material, it can be heavy and prone to corrosion. As a result, manufacturers began to experiment with different materials to improve the BCG’s performance.
One of the first materials to be used in AR15 BCGs was chrome plating. Chrome plating provides a hard, corrosion-resistant surface that reduces friction and wear on the BCG components. This not only improves the overall reliability of the AR15 but also extends the life of the BCG.
In recent years, manufacturers have started to use more advanced materials such as titanium and nickel boron in AR15 BCGs. Titanium is known for its strength-to-weight ratio, making it an ideal material for reducing the weight of the BCG without sacrificing durability. Nickel boron, on the other hand, is a self-lubricating material that reduces friction and wear on the BCG components, further enhancing the reliability of the AR15.
Another material that has gained popularity in AR15 BCGs is nitride. Nitride is a surface treatment that improves the hardness and corrosion resistance of the BCG components. It also provides a smooth surface that reduces friction and wear, resulting in improved performance and reliability.
Looking ahead, the future trends in materials used in AR15 BCGs are likely to focus on further improving the performance and durability of the BCG. One potential development is the use of carbon fiber reinforced polymers (CFRP) in BCG construction. CFRP is a lightweight and strong material that can help reduce the weight of the BCG while maintaining its durability.
Another trend to watch for is the use of advanced coatings such as DLC (diamond-like carbon) in AR15 BCGs. DLC coatings provide a hard, low-friction surface that enhances the performance and reliability of the BCG components. This technology is already being used in other firearms applications and is likely to make its way into AR15 BCGs in the near future.
In conclusion, the evolution of materials used in AR15 BCGs has played a significant role in improving the performance and reliability of the platform. From the early days of steel to the advanced materials used today, manufacturers continue to push the boundaries of what is possible with the AR15 BCG. As new materials and technologies emerge, we can expect to see even greater advancements in the future, further enhancing the capabilities of this iconic firearm.
Changes in Design and Functionality of AR15 BCG
The AR15 Bolt Carrier Group (BCG) has undergone significant changes in design and functionality since its inception. Originally developed for military use in the 1950s, the AR15 BCG has evolved over the years to meet the demands of civilian shooters and law enforcement agencies. In this article, we will explore the historical developments of the AR15 BCG and discuss future trends in its design and functionality.
One of the most significant changes in the design of the AR15 BCG is the introduction of different coatings and finishes. Early BCGs were typically made of steel and required regular maintenance to prevent corrosion. However, advancements in coating technology have led to the development of BCGs with durable finishes such as nickel boron and nitride. These coatings provide increased lubricity and corrosion resistance, making them ideal for high-volume shooting.
Another key development in the evolution of the AR15 BCG is the introduction of lightweight materials. Traditional BCGs were made of steel, which added weight to the rifle and increased felt recoil. In response to this, manufacturers began producing BCGs made of aluminum and titanium, reducing the overall weight of the rifle without sacrificing durability. Lightweight BCGs are particularly popular among competition shooters who value fast target acquisition and reduced fatigue during extended shooting sessions.
In addition to changes in materials and coatings, the design of the AR15 BCG has also evolved to improve reliability and performance. One notable innovation is the addition of forward assist serrations on the BCG, allowing shooters to manually push the bolt into battery in the event of a malfunction. This feature has become standard on many modern BCGs and is considered essential for shooters who require a high level of reliability in their firearms.
Furthermore, advancements in machining technology have enabled manufacturers to produce BCGs with tighter tolerances and improved consistency. This has led to increased accuracy and reliability in AR15 rifles, making them a popular choice for both recreational and professional shooters. Additionally, the use of enhanced extractor designs and improved gas rings has further improved the reliability of the AR15 BCG, reducing the likelihood of malfunctions during shooting.
Looking towards the future, it is likely that we will continue to see advancements in the design and functionality of the AR15 BCG. Manufacturers are constantly exploring new materials and coatings to improve performance and durability, while also seeking ways to reduce weight and increase reliability. Additionally, advancements in computer-aided design and manufacturing technology will allow for even tighter tolerances and improved consistency in BCG production.
In conclusion, the AR15 BCG has come a long way since its introduction in the 1950s. Through advancements in materials, coatings, and design, the AR15 BCG has become a reliable and high-performing component of the modern sporting rifle. As technology continues to evolve, we can expect to see further improvements in the design and functionality of the AR15 BCG, making it an even more versatile and effective tool for shooters of all skill levels.
Impact of Technology on AR15 BCG Development
The AR15 Bolt Carrier Group (BCG) has undergone significant evolution over the years, driven by advancements in technology and the demands of modern shooters. The BCG is a critical component of the AR15 platform, responsible for cycling rounds, extracting spent casings, and loading new rounds into the chamber. As such, improvements in BCG design have a direct impact on the performance and reliability of the rifle.
One of the key developments in AR15 BCG technology was the introduction of the full-auto BCG. Originally designed for military and law enforcement applications, the full-auto BCG features a heavier profile and increased mass to enhance reliability in fully automatic or burst-fire rifles. While not necessary for semi-automatic rifles, many civilian shooters have adopted the full-auto BCG for its perceived benefits in terms of durability and reduced recoil.
Another significant advancement in AR15 BCG technology was the introduction of coatings and finishes to improve wear resistance and reduce friction. Traditional BCGs were typically made from carbon steel or stainless steel, which required regular lubrication to prevent corrosion and ensure smooth operation. However, modern BCGs are often coated with materials such as nickel boron, titanium nitride, or DLC (Diamond-Like Carbon) to enhance durability and reduce the need for lubrication.
In addition to coatings and finishes, manufacturers have also experimented with alternative materials for AR15 BCGs. For example, some BCGs are now made from lightweight materials such as aluminum or titanium to reduce overall weight and improve handling. While these materials may not be as durable as steel, they offer a significant weight savings for shooters who prioritize mobility and maneuverability.
The latest trend in AR15 BCG development is the integration of advanced features such as adjustable gas systems, enhanced bolt designs, and improved extraction mechanisms. Adjustable gas systems allow shooters to fine-tune the amount of gas directed to the BCG, which can help reduce recoil, improve reliability, and optimize performance with different types of ammunition. Enhanced bolt designs, such as dual ejectors or improved lug geometry, can also contribute to smoother cycling and increased durability.
Looking ahead, the future of AR15 BCG development is likely to be shaped by advancements in materials science, manufacturing techniques, and firearm technology. For example, the use of 3D printing technology could revolutionize the production of BCGs, allowing for complex geometries and custom designs that were previously impossible with traditional machining methods. Additionally, advancements in metallurgy could lead to the development of new alloys with superior strength, durability, and corrosion resistance.
Overall, the evolution of the AR15 BCG is a testament to the ingenuity and innovation of the firearms industry. As technology continues to advance, shooters can expect to see further improvements in BCG design that will enhance the performance and reliability of their rifles. Whether it’s through the adoption of new materials, coatings, or features, the AR15 BCG will continue to evolve to meet the needs of modern shooters.
Future Trends in AR15 BCG Innovation
The AR15 Bolt Carrier Group (BCG) has undergone significant evolution since its inception, with advancements in materials, coatings, and design leading to improved performance and reliability. As the popularity of the AR15 platform continues to grow, manufacturers are constantly pushing the boundaries of innovation to meet the demands of shooters looking for the latest and greatest in BCG technology.
One of the most notable trends in AR15 BCG innovation is the use of advanced materials such as titanium and nickel boron. These materials offer increased durability, reduced friction, and improved corrosion resistance compared to traditional steel BCGs. Titanium BCGs, in particular, are known for their lightweight construction and high strength-to-weight ratio, making them a popular choice among shooters looking to reduce the overall weight of their rifle without sacrificing performance.
Another trend in AR15 BCG innovation is the development of enhanced coatings such as nitride, DLC (Diamond-Like Carbon), and PVD (Physical Vapor Deposition). These coatings provide a hard, slick surface that reduces friction and wear, resulting in smoother cycling and increased reliability. Nitride coatings, in particular, have gained popularity for their excellent corrosion resistance and long-lasting durability, making them a top choice for shooters looking for a low-maintenance BCG that can withstand harsh environmental conditions.
In addition to materials and coatings, design improvements have also played a significant role in the evolution of the AR15 BCG. One of the most notable design trends is the use of dual ejectors and enhanced extractor springs, which provide increased reliability in extracting and ejecting spent casings. These design features help prevent malfunctions such as stovepipes and double feeds, ensuring smooth and consistent cycling even in adverse conditions.
Another design trend in AR15 BCG innovation is the incorporation of adjustable gas keys and weight systems. These features allow shooters to fine-tune their rifle’s gas system for optimal performance, reducing recoil and muzzle rise while maintaining reliable cycling. Adjustable gas keys also make it easier to tune the rifle for different ammunition types or shooting conditions, providing greater versatility and customization options for shooters.
Looking ahead, the future of AR15 BCG innovation is likely to focus on further advancements in materials, coatings, and design to continue improving performance and reliability. Manufacturers are constantly researching and developing new technologies to push the boundaries of what is possible with the AR15 platform, with a focus on reducing weight, increasing durability, and enhancing overall functionality.
As shooters continue to demand the best in AR15 BCG technology, manufacturers will undoubtedly rise to the challenge by introducing new and innovative products that push the limits of performance and reliability. Whether it’s through the use of advanced materials, enhanced coatings, or cutting-edge design features, the evolution of the AR15 BCG is sure to continue shaping the future of the platform for years to come.