“Material Matters: Unleash Peak Performance with Premium Rifle Bolt Alloys”
Understanding the Durability: Top Alloys for Rifle Bolt Construction
Material Matters: The Best Alloys for Your Rifle Bolt
When it comes to the construction of a rifle bolt, the choice of material is not just a matter of preference but a critical decision that affects the performance, durability, and safety of the firearm. The bolt is the heart of a rifle’s action, enduring extreme pressures and friction each time the gun is fired. Consequently, selecting the right alloy for your rifle bolt is paramount to ensure that it can withstand the rigors of use while maintaining precision and reliability.
The quest for the ideal rifle bolt material has led to the development and utilization of various alloys, each offering a unique blend of properties. Among the most favored materials in the industry are stainless steel, carbon steel, and titanium alloys, each bringing its own advantages to the table.
Stainless steel is a popular choice for rifle bolts due to its excellent corrosion resistance. This characteristic is particularly beneficial for hunters and shooters who frequently expose their rifles to harsh weather conditions. Stainless steel bolts can resist rust and corrosion without the need for additional coatings, which can wear off over time. Moreover, stainless steel provides a good balance of strength and ductility, making it tough enough to handle repeated cycling without becoming brittle.
Transitioning to carbon steel, this material is known for its superior strength and hardness. Carbon steel bolts are less expensive than their stainless counterparts, making them an attractive option for those who prioritize durability and cost-effectiveness. The higher carbon content in these alloys contributes to their increased wear resistance, which is crucial for the longevity of the bolt. However, carbon steel is more susceptible to corrosion, so protective finishes like bluing or nitriding are often applied to extend the life of the bolt.
Another high-performance option is titanium, an alloy revered for its exceptional strength-to-weight ratio. Titanium bolts are significantly lighter than those made from steel, which can be a boon for reducing the overall weight of a rifle. This reduction in weight does not come at the expense of durability; titanium is incredibly strong and can withstand extreme temperatures and pressures. Its natural resistance to corrosion also means that titanium bolts require less maintenance. However, the cost of titanium is considerably higher than steel, which can be a limiting factor for some users.
When choosing the best alloy for a rifle bolt, it’s also important to consider the manufacturing process. Precision machining is essential to ensure that the bolt fits perfectly within the rifle’s action and operates smoothly. The material’s machinability plays a significant role in the quality of the final product. Stainless steel and carbon steel are generally easier to machine than titanium, which requires specialized equipment and expertise.
In conclusion, the selection of the right alloy for a rifle bolt is a nuanced decision that hinges on a balance of properties such as strength, corrosion resistance, weight, and cost. Stainless steel offers a middle ground with good strength and excellent corrosion resistance. Carbon steel is favored for its hardness and cost-effectiveness but requires protective finishes. Titanium stands out for its lightweight and superior strength but comes at a higher price point. Ultimately, the best alloy for your rifle bolt will depend on your specific needs, preferences, and the conditions in which your rifle will be used. By understanding the unique attributes of these top alloys, you can make an informed decision that ensures the longevity and reliability of your firearm.
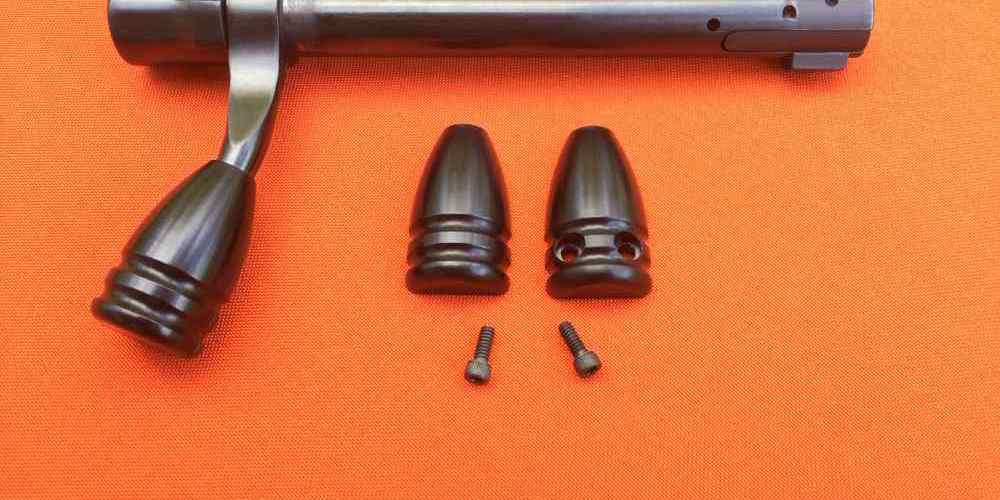
Balancing Strength and Weight: Selecting the Ideal Alloy for Your Rifle Bolt
Material Matters: The Best Alloys for Your Rifle Bolt
When it comes to the performance and longevity of a rifle, the quality of its components is paramount. Among these, the rifle bolt is a critical part that demands careful consideration of material choice. The bolt is the heart of a rifle’s action, enduring the brunt of the firing cycle’s stress. Therefore, selecting the ideal alloy for your rifle bolt is a delicate balance between strength and weight, ensuring reliability without compromising the firearm’s handling.
Alloys are mixtures of metals that are engineered to exhibit specific properties, such as increased strength, corrosion resistance, or lighter weight. For rifle bolts, the material must be robust enough to handle the repeated force of the cartridge ignition while maintaining a weight that keeps the rifle balanced and easy to handle. This is where the science of metallurgy shines, offering a range of alloys that can be tailored to meet these exacting requirements.
One of the most popular choices for high-strength applications is 4340 steel, an alloy known for its outstanding toughness and high tensile strength. This material can withstand the significant pressures exerted by modern cartridges, making it a reliable choice for a rifle bolt. Its composition, which includes nickel, chromium, and molybdenum, contributes to its impressive hardenability and resistance to wear. However, 4340 steel is relatively heavy, which may be a drawback for those seeking to minimize the weight of their rifle.
In contrast, titanium alloys present an attractive alternative for those prioritizing weight reduction without a significant sacrifice in strength. Titanium is approximately 45% lighter than steel and exhibits exceptional corrosion resistance, which is beneficial for rifles used in harsh environments. A titanium bolt can reduce the overall weight of the rifle, improving maneuverability and reducing shooter fatigue during extended use. However, the trade-off is cost, as titanium is more expensive than steel and more challenging to machine, which can increase the price of the finished bolt.
Another contender is 7075 aluminum, an alloy commonly used in aerospace applications due to its high strength-to-weight ratio. While not as strong as steel or titanium, 7075 aluminum can be an excellent choice for less demanding applications or for competition rifles where weight savings are crucial. This alloy is often treated with an anodizing process to enhance its surface hardness and corrosion resistance, making it more suitable for use in a rifle bolt.
Ultimately, the best alloy for a rifle bolt depends on the specific needs and preferences of the shooter. For those who require uncompromising strength and durability, a steel alloy like 4340 may be the best choice. For hunters or competitive shooters who value a lightweight rifle for ease of carry and quick handling, titanium or 7075 aluminum may be more appropriate.
In conclusion, the selection of the ideal alloy for a rifle bolt is a nuanced decision that requires a thorough understanding of the trade-offs between strength, weight, and cost. Whether opting for the ruggedness of steel, the lightness of titanium, or the balance offered by aluminum, shooters must consider their individual requirements and the demands of their shooting discipline. By carefully choosing the right material, one can ensure that their rifle performs reliably shot after shot, providing the confidence needed to excel in any shooting endeavor.
Corrosion Resistance: Choosing Alloys That Endure for Rifle Bolts
Material Matters: The Best Alloys for Your Rifle Bolt
When it comes to the longevity and reliability of firearms, the choice of materials is paramount, especially for components subjected to high stress and environmental exposure, such as the rifle bolt. The bolt is the heart of a rifle’s action, enduring the brunt of mechanical stress and corrosive elements. Therefore, selecting an alloy with superior corrosion resistance is not just a matter of performance but also of safety and durability.
Corrosion resistance in rifle bolts is critical because it ensures that the firearm remains functional and safe over time, even under adverse conditions. Corrosion can compromise the structural integrity of the bolt, leading to potential failure and, consequently, posing a risk to the user. To mitigate these risks, manufacturers often turn to high-grade alloys known for their ability to withstand corrosive environments.
Stainless steel is a popular choice for rifle bolts due to its excellent corrosion resistance. Alloys such as 416 and 17-4PH stainless steel are frequently used in the firearms industry. The 416 grade offers good machinability, which is essential for manufacturing complex bolt shapes, while 17-4PH provides enhanced strength and hardness through heat treatment, making it an ideal candidate for high-stress applications.
Another alloy that stands out in the realm of rifle bolts is the maraging steel series, particularly grades like 300 and 350. These steels are known for their ultra-high strength and toughness, which are achieved through a unique aging process. While they may not be as inherently corrosion-resistant as some stainless steels, their mechanical properties make them excellent choices for precision shooting and military applications where strength is a priority. To enhance their corrosion resistance, these alloys can be coated or treated with surface finishing processes.
Titanium alloys also deserve mention for their exceptional strength-to-weight ratio and corrosion resistance. Alloys such as Ti-6Al-4V are commonly used in aerospace and medical industries but have found their way into the manufacturing of high-end rifle bolts. Titanium offers the advantage of being lighter than steel, which can be beneficial for reducing the overall weight of the firearm without compromising the bolt’s integrity.
In selecting the right alloy for a rifle bolt, it’s essential to consider the specific needs of the firearm and its intended use. For instance, a hunting rifle exposed to harsh weather conditions might benefit from a stainless steel bolt, while a competition rifle where weight savings are crucial could be better served with a titanium bolt.
Moreover, the manufacturing process and the ability to achieve tight tolerances are also factors to consider. Alloys that are more machinable allow for the precise fabrication of bolt components, ensuring a perfect fit and smooth operation within the rifle’s action. This precision is crucial for maintaining the firearm’s accuracy and reliability over time.
In conclusion, the best alloy for a rifle bolt is one that offers a balance between corrosion resistance, mechanical strength, and manufacturability. Whether it’s the proven performance of stainless steel, the robustness of maraging steel, or the lightweight resilience of titanium, the choice of material will significantly impact the rifle’s endurance and functionality. As technology advances and new alloys are developed, the quest for the perfect rifle bolt material continues, always with the aim of achieving the highest standards of safety, performance, and longevity.
Precision Shooting: How Alloy Choice Affects Rifle Bolt Performance
Material Matters: The Best Alloys for Your Rifle Bolt
Precision shooting is an art that demands not only skill and patience but also the finest equipment. One critical component that often gets overlooked is the rifle bolt. The bolt is the heart of a rifle’s action, and its performance can significantly affect accuracy and reliability. The choice of material for your rifle bolt is paramount, and selecting the best alloy can make all the difference in your shooting experience.
Alloys are mixtures of metals that are engineered to have specific properties, such as strength, hardness, and resistance to wear and corrosion. For rifle bolts, these characteristics are essential for enduring the repeated stress of firing and the harsh environmental conditions they may be exposed to. The right alloy will ensure that your bolt operates smoothly, maintains its shape, and provides a consistent lockup with the chamber, all of which contribute to the precision of your shots.
One of the most popular materials for high-performance rifle bolts is 4140 steel, also known as Chromoly steel. This alloy is renowned for its outstanding tensile strength and toughness, which are crucial for withstanding the explosive forces of a fired cartridge. Moreover, 4140 steel has excellent fatigue resistance, meaning it can endure the cyclical loading and unloading of rounds without losing its structural integrity. This resilience makes it an ideal choice for shooters who demand reliability from their equipment.
Transitioning to another exceptional material, 4340 steel is often considered an upgrade from 4140. It contains more nickel, chromium, and molybdenum, which enhances its already impressive strength and toughness. The addition of these elements also improves its resistance to shock and wear, making 4340 steel bolts even more durable. For those who frequently shoot high-powered cartridges or engage in extreme long-range shooting, this alloy offers the extra assurance that their bolt will perform flawlessly shot after shot.
Stainless steel is another contender in the realm of rifle bolt materials. Alloys such as 17-4 PH stainless steel provide excellent corrosion resistance, which is particularly beneficial for shooters who operate in humid or marine environments. This material also maintains its strength across a wide range of temperatures, ensuring consistent performance whether you’re shooting in the freezing cold or under the scorching sun. Stainless steel bolts are not only functional but also have an aesthetic appeal, with their natural silver finish giving a rifle a sleek, professional look.
For the ultimate in lightweight performance, titanium alloys are the pinnacle. Titanium is nearly as strong as steel but roughly 45% lighter, which can be a significant advantage for those who need to carry their rifle over long distances or aim for extended periods without fatigue. Titanium bolts also exhibit excellent corrosion resistance and can withstand extreme temperatures. However, this high-end material comes at a premium cost, making it a choice for those who prioritize weight savings and are willing to invest in top-tier equipment.
In conclusion, the alloy you choose for your rifle bolt can have a profound impact on your shooting experience. Whether you opt for the robust and reliable 4140 or 4340 steel, the corrosion-resistant and stylish stainless steel, or the lightweight and high-performing titanium, each material offers unique benefits. As a precision shooter, it’s essential to consider your specific needs and preferences when selecting an alloy for your rifle bolt. The right choice will provide you with a bolt that not only enhances your rifle’s performance but also stands the test of time, allowing you to focus on perfecting your shot with confidence.
The Evolution of Rifle Bolt Materials: From Steel to Advanced Alloys
Material Matters: The Best Alloys for Your Rifle Bolt
The rifle bolt is the heart of any bolt-action rifle, and its material composition is critical for performance, durability, and safety. Over the years, the evolution of rifle bolt materials has seen a transition from simple steels to advanced alloys, each offering unique benefits and challenges. In this exploration of the best alloys for your rifle bolt, we’ll delve into the technical aspects that make certain materials stand out in the demanding world of firearms.
Traditionally, rifle bolts were crafted from high-grade steel, prized for its strength and resilience. Steel’s robust nature made it an obvious choice, ensuring that the bolt could withstand the pressures generated by the firing process. However, as technology advanced, the quest for lighter, stronger, and more corrosion-resistant materials led to the development of specialized alloys.
One such material that has gained prominence in the manufacturing of rifle bolts is stainless steel. This alloy, which incorporates elements like chromium, nickel, and molybdenum, offers enhanced resistance to rust and corrosion compared to its carbon steel counterparts. This makes stainless steel bolts particularly well-suited for use in harsh environments where moisture and corrosive elements are a concern. Moreover, the addition of these alloying elements does not compromise the strength of the bolt, ensuring that it remains reliable under stress.
Another contender in the realm of advanced alloys is titanium. Known for its exceptional strength-to-weight ratio, titanium bolts are significantly lighter than those made from steel, which can be a boon for hunters and marksmen who value a lightweight rifle for ease of handling and transport. Despite its reduced weight, titanium maintains impressive tensile strength, though it is typically more expensive and can be more challenging to machine than steel.
The aerospace industry has also contributed to the development of rifle bolt materials with the introduction of maraging steels. These are a unique class of ultra-high-strength steels that undergo an aging process to achieve superior toughness and strength without losing malleability. Maraging steel bolts are characterized by their ability to absorb significant stress without permanent deformation, making them an excellent choice for high-performance rifles that demand reliability under extreme conditions.
In recent years, the firearms industry has also seen the emergence of metal matrix composites (MMCs). These materials combine metal with other elements, such as ceramic particles, to create a composite that can be fine-tuned for specific properties. MMCs can be engineered to offer a balance of lightness, thermal stability, and wear resistance, which are critical factors for a rifle bolt that experiences rapid temperature changes and friction during operation.
When selecting the best alloy for a rifle bolt, it is essential to consider the intended use of the firearm. For instance, a competitive shooter might prioritize the weight savings of a titanium bolt, while a hunter in coastal areas might opt for the corrosion resistance of stainless steel. Similarly, a military sniper might rely on the ruggedness and consistency of a maraging steel bolt for missions that demand unwavering performance.
In conclusion, the choice of material for a rifle bolt is not one to be taken lightly. The evolution from steel to advanced alloys has opened up a world of possibilities, each with its own set of advantages. Whether it’s the corrosion resistance of stainless steel, the lightweight nature of titanium, the toughness of maraging steel, or the tailored properties of MMCs, the right alloy can significantly enhance the functionality and longevity of your rifle. As materials science continues to advance, we can only expect to see further innovations in rifle bolt technology, ensuring that shooters have access to the best possible materials for their needs.