“From raw materials to precision engineering, witness the creation of the ultimate firearm component.”
The History of AR15 Lower Receivers
The AR15 is one of the most popular rifles in the United States, known for its versatility, accuracy, and customization options. One of the key components of an AR15 is the lower receiver, which is the part of the rifle that houses the trigger group and magazine well. The lower receiver is also the only part of the AR15 that is considered a firearm by the ATF, making it a crucial component in the manufacturing process.
The process of making an AR15 lower receiver begins with casting. Casting is a manufacturing process in which molten metal is poured into a mold and allowed to cool and solidify. The most common material used for casting AR15 lower receivers is aluminum, specifically 7075-T6 aluminum, which is known for its strength and durability. Once the aluminum has been cast, it is then machined to remove any excess material and to create the final shape of the lower receiver.
After the lower receiver has been cast and machined, it is then sent to be heat treated. Heat treating is a process in which the metal is heated to a specific temperature and then cooled rapidly to increase its strength and hardness. This is an important step in the manufacturing process, as it ensures that the lower receiver will be able to withstand the stresses and pressures of firing a rifle.
Once the lower receiver has been heat treated, it is then sent to be anodized. Anodizing is a process in which a protective oxide layer is applied to the surface of the aluminum to increase its corrosion resistance and durability. The most common type of anodizing used for AR15 lower receivers is Type III hardcoat anodizing, which is known for its toughness and abrasion resistance.
After the lower receiver has been anodized, it is then sent to be engraved with the manufacturer’s information and serial number. This information is required by law, as all firearms must be serialized and registered with the ATF. The engraving process is typically done using a laser engraver, which allows for precise and detailed markings to be made on the surface of the lower receiver.
Once the lower receiver has been engraved, it is then sent to be assembled with the other components of the AR15. This includes attaching the upper receiver, barrel, stock, and other parts to create a fully functioning rifle. The final step in the manufacturing process is to test fire the rifle to ensure that it functions properly and meets all safety and performance standards.
In conclusion, the process of making an AR15 lower receiver is a complex and precise one that requires careful attention to detail and quality control. From casting to firing, each step in the manufacturing process plays a crucial role in creating a high-quality and reliable firearm. The history of AR15 lower receivers is a testament to the ingenuity and craftsmanship of the manufacturers who produce these essential components for one of the most iconic rifles in American history.
The Casting Process for AR15 Lower Receivers
The process of making an AR15 lower receiver is a complex and intricate one that involves several steps, starting with casting. Casting is the process of pouring molten metal into a mold to create a specific shape. In the case of AR15 lower receivers, the metal used is typically aluminum, as it is lightweight yet strong enough to withstand the pressures and forces of firing a rifle.
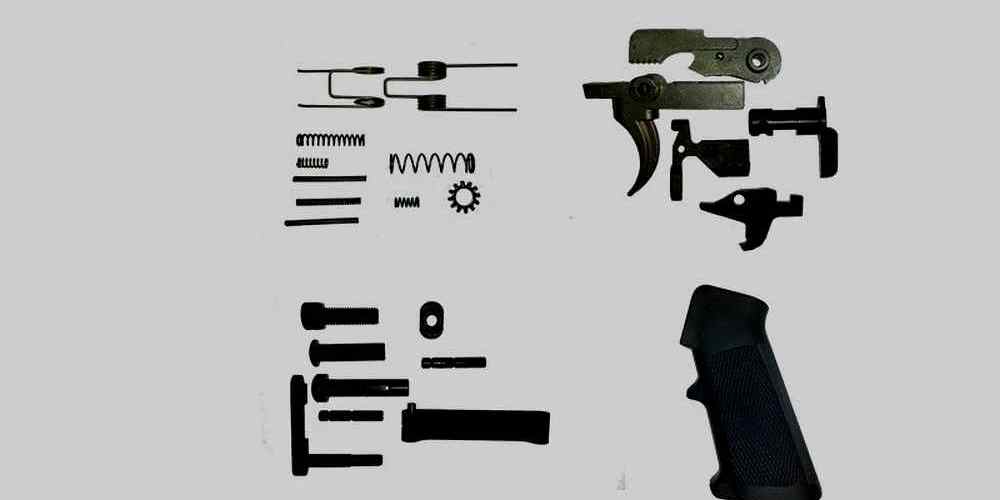
The first step in the casting process is to create a mold of the lower receiver. This mold is typically made from a material such as sand or plaster, which is packed around a model of the lower receiver. Once the mold is created, it is heated to a high temperature to remove any moisture and ensure that the metal will flow smoothly into the mold.
Next, the aluminum is melted in a furnace and poured into the mold. The molten metal fills the mold and takes on the shape of the lower receiver. Once the metal has cooled and solidified, the mold is removed, revealing the rough shape of the lower receiver.
The next step in the process is to machine the rough casting to its final dimensions. This involves using a variety of tools and techniques to remove excess material and shape the lower receiver to its final form. This process requires precision and skill to ensure that the lower receiver meets the exact specifications required for proper function.
After the lower receiver has been machined, it is then heat treated to strengthen the metal and improve its durability. This involves heating the lower receiver to a specific temperature and then cooling it slowly to relieve any internal stresses and improve the overall strength of the metal.
Once the lower receiver has been heat treated, it is then coated with a protective finish to prevent corrosion and improve its appearance. This finish can be applied through a variety of methods, such as anodizing or painting, depending on the desired look and function of the lower receiver.
Overall, the process of casting an AR15 lower receiver is a complex and precise one that requires skill and attention to detail. From creating the mold to machining the rough casting to applying the final finish, each step plays a crucial role in creating a high-quality lower receiver that is both functional and durable.
In conclusion, the casting process for AR15 lower receivers is just the first step in a series of processes that ultimately result in a finished product ready for use. By understanding the intricacies of this process, gun enthusiasts can gain a greater appreciation for the craftsmanship and skill that goes into creating these essential components of a rifle.
Machining Techniques for AR15 Lower Receivers
When it comes to building your own AR15, one of the most crucial components is the lower receiver. This is the part of the firearm that houses the trigger group, magazine well, and buffer tube, making it essential for the overall functionality of the rifle. While you can purchase a lower receiver ready-made, many gun enthusiasts prefer to build their own from scratch. In this article, we will take you through the process of making an AR15 lower receiver, from casting to firing.
The first step in creating an AR15 lower receiver is casting the raw material. Most lower receivers are made from aluminum, as it is lightweight, durable, and easy to work with. The casting process involves pouring molten aluminum into a mold that is shaped like the lower receiver. Once the aluminum has cooled and solidified, the mold is removed, leaving behind a rough casting of the lower receiver.
Next comes the machining process, where the rough casting is transformed into a finished lower receiver. This involves using a variety of tools, such as CNC machines, mills, and lathes, to cut away excess material and shape the receiver to its final dimensions. This step requires precision and attention to detail, as even the smallest error can affect the functionality of the firearm.
One of the most critical aspects of machining an AR15 lower receiver is ensuring that the dimensions are within spec. This is important because the lower receiver must fit with other components of the rifle, such as the upper receiver and buffer tube. If the dimensions are off, it can lead to malfunctions and poor performance. To avoid this, machinists use precise measurements and tools to ensure that the receiver meets the required specifications.
In addition to dimensions, the machining process also involves creating the necessary features on the lower receiver, such as the magazine well, trigger guard, and selector switch hole. These features are essential for the functionality of the firearm, so they must be carefully machined to ensure proper operation. Machinists use specialized tools and techniques to create these features accurately and efficiently.
Once the machining process is complete, the lower receiver is ready for finishing. This involves applying a coating to the receiver to protect it from corrosion and wear. There are several options for finishing, including anodizing, cerakoting, and painting. Each method has its advantages and disadvantages, so it is essential to choose the right finish for your needs.
After finishing, the lower receiver is assembled with the other components of the AR15, such as the upper receiver, barrel, and stock. Once fully assembled, the rifle is ready for testing and firing. It is essential to test the firearm to ensure that it functions correctly and safely. This involves checking for proper cycling, accuracy, and reliability.
In conclusion, the process of making an AR15 lower receiver is a complex and intricate one that requires skill, precision, and attention to detail. From casting to firing, each step plays a crucial role in creating a functional and reliable firearm. By following the proper techniques and using the right tools, you can build your own AR15 lower receiver with confidence and pride.
Quality Control and Testing of AR15 Lower Receivers
When it comes to building an AR15, one of the most critical components is the lower receiver. This part serves as the foundation for the entire firearm, housing the trigger group, magazine well, and buffer tube. The process of manufacturing an AR15 lower receiver involves several steps, from casting to firing, to ensure that the final product meets the highest quality standards.
The first step in making an AR15 lower receiver is casting. This process involves pouring molten aluminum into a mold to create the basic shape of the receiver. The aluminum used in this process is typically a high-strength alloy, such as 7075-T6, which provides the necessary durability and strength for the receiver to withstand the rigors of firing.
Once the receiver has been cast, it undergoes a series of machining operations to refine its shape and dimensions. This includes drilling holes for the trigger group, magazine well, and buffer tube, as well as milling out excess material to reduce weight and improve ergonomics. Precision is key in this step, as even minor deviations from the design specifications can affect the performance and reliability of the firearm.
After machining, the receiver is subjected to a series of quality control checks to ensure that it meets the required standards. This includes dimensional inspections to verify that the receiver’s dimensions are within tolerance, as well as visual inspections to check for any surface defects or imperfections. Any parts that do not meet the specified criteria are rejected and either reworked or scrapped.
Once the receiver has passed all quality control checks, it undergoes a series of finishing operations to prepare it for assembly. This includes applying a protective coating, such as anodizing or Cerakote, to enhance its durability and corrosion resistance. The receiver is then laser-engraved with the manufacturer’s logo, serial number, and other identifying information required by law.
With the receiver now complete, it is ready for assembly into a complete firearm. This involves installing the trigger group, magazine well, buffer tube, and other components to create a functional AR15. Once assembled, the firearm is subjected to a series of function tests to ensure that it operates correctly and reliably. This includes checking the trigger pull, magazine insertion and ejection, and overall functionality of the firearm.
After assembly, the AR15 undergoes a series of firing tests to verify its performance and reliability. This includes test-firing the firearm with a variety of ammunition types and checking for any malfunctions or issues. The firearm is also subjected to a series of endurance tests to simulate real-world use and ensure that it can withstand the demands of regular shooting.
In conclusion, the process of making an AR15 lower receiver is a complex and precise undertaking that requires careful attention to detail and quality control. From casting to firing, each step in the manufacturing process plays a crucial role in ensuring that the final product meets the highest standards of performance and reliability. By following strict quality control procedures and testing protocols, manufacturers can produce AR15 lower receivers that are not only durable and reliable but also safe for use by firearm enthusiasts and professionals alike.
The Legalities of Manufacturing AR15 Lower Receivers
When it comes to manufacturing firearms, there are a lot of legal considerations that need to be taken into account. This is especially true when it comes to the production of AR15 lower receivers. In the United States, the Bureau of Alcohol, Tobacco, Firearms and Explosives (ATF) regulates the manufacturing of firearms, including lower receivers.
One of the most important things to keep in mind when manufacturing AR15 lower receivers is that they are considered firearms under federal law. This means that anyone who wants to manufacture AR15 lower receivers needs to have a Federal Firearms License (FFL). Without an FFL, it is illegal to manufacture AR15 lower receivers for sale or distribution.
In addition to having an FFL, manufacturers of AR15 lower receivers also need to comply with all federal, state, and local laws regarding firearms manufacturing. This includes following regulations related to background checks, record keeping, and serial number engraving. Failure to comply with these laws can result in serious legal consequences, including fines and imprisonment.
Another important legal consideration when manufacturing AR15 lower receivers is ensuring that the receivers are compliant with the National Firearms Act (NFA). The NFA regulates the sale and possession of certain firearms, including short-barreled rifles and machine guns. AR15 lower receivers that are not compliant with the NFA can result in criminal charges for both the manufacturer and the end user.
To ensure compliance with the NFA, manufacturers of AR15 lower receivers need to be aware of the specific requirements for these firearms. This includes ensuring that the receiver is not capable of accepting a fully automatic fire control group, as this would classify it as a machine gun under the NFA. Additionally, manufacturers need to be aware of any state-specific regulations that may apply to the production of AR15 lower receivers.
Overall, the legalities of manufacturing AR15 lower receivers are complex and require careful attention to detail. By obtaining an FFL, following all federal, state, and local laws, and ensuring compliance with the NFA, manufacturers can avoid legal issues and produce high-quality AR15 lower receivers that are safe and legal for consumers to use.
In conclusion, the legalities of manufacturing AR15 lower receivers are an important consideration for anyone looking to enter the firearms manufacturing industry. By understanding and complying with all relevant laws and regulations, manufacturers can ensure that their products are legal and safe for consumers to use. With the right knowledge and attention to detail, manufacturing AR15 lower receivers can be a rewarding and successful endeavor.