“Barrel Coatings and Finishes: Unleashing Superior Endurance and Precision”
The Top Barrel Coatings for Improved Corrosion Resistance
Barrel Coatings and Finishes: Enhancing Durability and Performance
In the world of firearms, the longevity and reliability of a barrel are paramount. As such, the industry has continually innovated with various coatings and finishes designed to enhance the durability and performance of barrels. These treatments not only protect against the natural elements but also reduce wear from mechanical action and resist the corrosive effects of gunpowder and cleaning chemicals. Among the plethora of options available, certain barrel coatings stand out for their superior corrosion resistance.
One of the top contenders in this arena is the application of Cerakote, a ceramic-based coating that has gained widespread acclaim for its exceptional hardness and resistance to abrasion. Cerakote forms a thin yet robust layer on the barrel’s surface, effectively shielding it from moisture and corrosive substances. Moreover, its ability to adhere to metal surfaces ensures a long-lasting finish that does not easily chip or wear away. This makes it an ideal choice for firearms that are frequently used in harsh environments or subjected to rigorous handling.
Transitioning from ceramic-based options, another highly regarded solution is the use of nitride treatments, such as Ferritic Nitrocarburizing (FNC). This thermochemical process infuses nitrogen and carbon into the surface of the steel, creating a hardened exterior that is remarkably resistant to corrosion. Unlike coatings that add a layer on top of the metal, nitriding alters the actual surface, which means there’s no risk of the coating peeling or flaking off. The result is a sleek, black finish that not only enhances the barrel’s resistance to rust but also improves its overall wear resistance.
Phosphate coatings, commonly referred to as Parkerizing, have been a traditional choice for military firearms due to their proven track record in preventing corrosion. The process involves immersing the barrel in a solution of phosphoric acid and other chemicals, which leads to the formation of a layer of crystalline phosphates on the metal surface. This layer serves as a sacrificial barrier, protecting the underlying metal from oxidation. While not as hard as Cerakote or as durable as nitriding, phosphate coatings offer a cost-effective solution that significantly improves corrosion resistance.
Moving forward, Physical Vapor Deposition (PVD) coatings are gaining traction for their unique properties. PVD coatings are applied in a vacuum chamber where metals are vaporized and then deposited onto the barrel’s surface. This results in a thin, uniform coating that can be harder than the substrate itself. PVD coatings are not only excellent at resisting corrosion but also reduce friction, which can lead to improved performance and easier cleaning.
Lastly, the use of Nickel-Boron (NiB) coatings is worth mentioning. This electroless plating process creates a layer of nickel alloy with boron, known for its incredible hardness and lubricity. NiB coatings not only resist corrosion but also create a self-lubricating surface that reduces the need for additional oils or lubricants. This can be particularly beneficial in reducing the buildup of carbon deposits and ensuring smoother action in the firearm’s operation.
In conclusion, the quest for improved corrosion resistance in firearm barrels has led to the development of various coatings and finishes, each with its own set of advantages. From the robust protection offered by Cerakote to the transformative properties of nitriding, and from the traditional reliability of phosphate coatings to the advanced technologies of PVD and NiB, gun owners and manufacturers have a wealth of options to choose from. These treatments not only extend the life of the barrel but also contribute to the firearm’s overall performance, ensuring that it remains a reliable tool for both professional and recreational use.
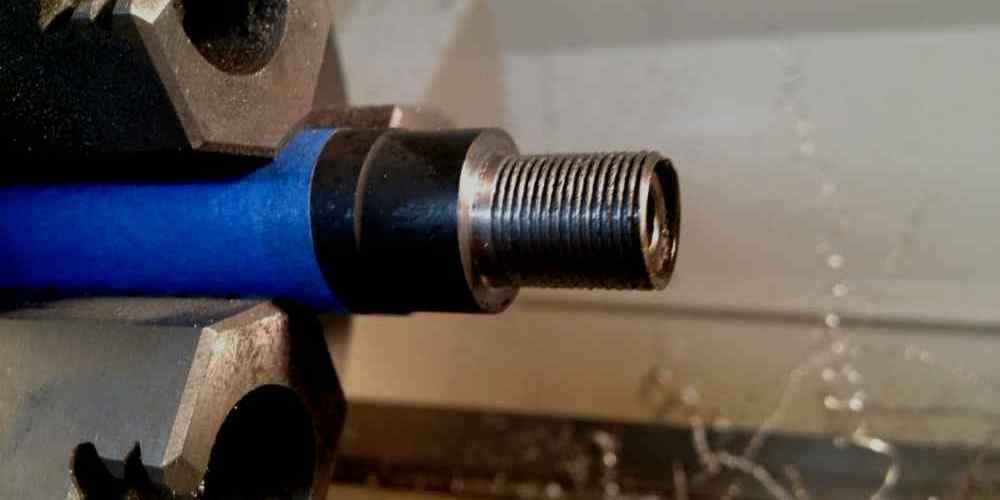
How Barrel Finishes Affect Firearm Accuracy and Maintenance
Barrel Coatings and Finishes: Enhancing Durability and Performance
In the world of firearms, the barrel is a critical component that directly influences accuracy, longevity, and overall performance. As such, the finishes and coatings applied to a barrel are not merely about aesthetics; they play a significant role in the firearm’s functionality. These treatments can affect everything from the ease of maintenance to the precision of shots fired, making them a key consideration for any gun owner or manufacturer.
One of the primary benefits of applying a finish to a firearm barrel is the protection it offers against the elements. Barrels are subjected to a variety of harsh conditions, including moisture, dirt, and the extreme heat generated with each shot. A quality finish, such as bluing, Parkerizing, or nitriding, can help to prevent rust and corrosion, which can otherwise lead to pitting and degradation of the barrel’s interior surface. This degradation can negatively impact the bullet’s trajectory as it travels down the barrel, resulting in decreased accuracy.
Moreover, certain finishes can reduce friction between the bullet and the barrel, which is crucial for maintaining a consistent shot pattern. For instance, nitride treatments not only protect against corrosion but also harden the surface of the barrel, making it more resistant to wear. This hardness ensures that the rifling inside the barrel, which imparts the necessary spin on the bullet, remains sharp and defined over time. A well-preserved rifling is essential for stabilizing the bullet in flight and achieving tight groupings on target.
Another aspect to consider is the ease of cleaning and maintenance that certain coatings can provide. A smoother, harder barrel surface is less likely to accumulate fouling and residue from gunpowder and bullet materials. This means that firearms with such coatings require less frequent cleaning, and when cleaning is necessary, the process is often more straightforward. A well-maintained barrel is key to preserving accuracy, as excessive buildup can alter the barrel’s internal dimensions and affect the bullet’s path.
In addition to these practical benefits, coatings and finishes can also enhance the overall performance of a firearm. For example, some finishes are designed to dissipate heat more effectively, which is particularly beneficial during rapid firing sessions. Excessive heat can lead to a phenomenon known as “barrel droop,” where the barrel’s material expands and shifts, impacting shot placement. Finishes that manage heat well help to mitigate this issue, maintaining accuracy even under strenuous firing conditions.
It’s important to note that not all finishes are created equal, and the choice of coating should be tailored to the firearm’s intended use. A hunting rifle exposed to outdoor elements might benefit most from a robust, corrosion-resistant finish, while a competition firearm might prioritize a finish that minimizes friction and heat buildup. Understanding the specific properties and advantages of each type of barrel finish allows gun owners and manufacturers to make informed decisions that enhance the performance and longevity of their firearms.
In conclusion, the impact of barrel coatings and finishes on firearm accuracy and maintenance cannot be overstated. By providing protection against wear and environmental damage, reducing friction, and facilitating easier maintenance, these treatments are essential for anyone looking to optimize their firearm’s performance. Whether for a seasoned marksman or a casual enthusiast, investing in a quality barrel finish is a wise decision that pays dividends in both the short and long term.
The Evolution of Barrel Coating Technologies in the Firearms Industry
Barrel Coatings and Finishes: Enhancing Durability and Performance
In the realm of firearms, the evolution of barrel coating technologies has been a game-changer in enhancing the durability and performance of guns. This progression has been driven by the relentless pursuit of reliability and longevity, which are critical factors for both recreational shooters and professionals alike. As we delve into the intricacies of these advancements, it becomes clear that the industry has come a long way from the traditional blued steel finishes of the past.
Initially, firearm barrels were treated with a process known as bluing, which involved a controlled oxidation of the steel to provide a degree of corrosion resistance and a classic aesthetic. However, as the demands on firearms increased, particularly in military and law enforcement applications, the need for more robust solutions became apparent. This led to the development of more advanced coatings that could withstand harsher environments and offer superior protection against wear and tear.
One of the most significant breakthroughs in barrel coatings has been the adoption of Physical Vapor Deposition (PVD) and Chemical Vapor Deposition (CVD) processes. These sophisticated techniques involve the deposition of thin films of materials such as nitrides, carbides, or diamond-like carbon onto the surface of the barrel. The result is a finish that is not only incredibly hard but also provides exceptional resistance to corrosion and abrasion. Moreover, these coatings reduce friction between the bullet and the barrel, which can lead to improved accuracy and a longer barrel life.
Another popular coating that has gained traction in the firearms industry is the use of polymer-based finishes, such as Teflon or Cerakote. These finishes are applied as a liquid and then cured to form a hard, protective layer over the metal. The versatility of polymer coatings allows for a wide range of colors and patterns, which can be both aesthetically pleasing and functional, as they can reduce glare or provide better camouflage. Additionally, these coatings are highly resistant to chemicals, making them ideal for use in environments where firearms may be exposed to harsh solvents or oils.
The application of advanced barrel coatings is not just limited to the exterior of the barrel. The interior, or bore, of the barrel can also benefit from these technologies. For instance, some manufacturers are now using a process called bore lining, where a super-hard material is deposited on the inside of the barrel. This lining reduces barrel wear from high-velocity rounds and can significantly extend the barrel’s service life.
As firearm enthusiasts and professionals continue to demand more from their equipment, the industry is responding with innovative solutions. The integration of nanotechnology into barrel coatings is one such frontier. Nanocoatings can provide a molecular-level finish that offers unparalleled protection and performance characteristics. These ultra-thin coatings can penetrate the smallest imperfections on the barrel’s surface, creating a barrier that is nearly impervious to the elements.
In conclusion, the evolution of barrel coating technologies in the firearms industry is a testament to the continuous quest for improvement. From the early days of simple bluing to the cutting-edge nanocoatings of today, each advancement represents a leap forward in firearm performance and durability. As these technologies continue to mature, we can expect to see even more impressive innovations that will further enhance the capabilities of firearms, ensuring that they remain reliable tools for sport, defense, and duty for years to come.
Comparing High-Performance Barrel Finishes: Cerakote vs. Nitride
Barrel Coatings and Finishes: Enhancing Durability and Performance
In the world of firearms, the longevity and performance of a gun barrel are paramount. To this end, various high-performance finishes have been developed to protect and enhance these critical components. Among the most popular and effective treatments are Cerakote and nitride coatings, each offering a unique set of benefits that cater to different needs and preferences within the shooting community.
Cerakote, a ceramic-based coating, has gained a reputation for its exceptional durability and resistance to wear. Applied as a liquid and then cured in an oven, Cerakote forms a hard layer that shields the barrel from the elements. This protective barrier is not only resistant to corrosion but also stands up to the abrasive forces encountered during cleaning and regular use. Moreover, Cerakote’s ability to adhere to a variety of materials makes it a versatile option for many firearm components beyond just the barrel.
Transitioning from the ceramic realm to the chemical, nitride finishes offer a different approach to barrel protection. Nitriding, which involves diffusing nitrogen into the steel, creates a surface that is incredibly hard and resistant to corrosion. Unlike Cerakote, nitride is not a coating but a treatment that modifies the surface layer of the metal itself. This process results in a sleek, black finish that is integral to the barrel, eliminating concerns about peeling or chipping that can occur with external coatings.
When comparing the two, it’s important to consider the specific demands of your shooting activities. Cerakote’s ability to withstand extreme temperatures and its vast color options make it a favorite among those who operate in harsh environments or desire a customized aesthetic. Its insulating properties can also be beneficial in maintaining barrel temperature, which can be crucial for precision shooters.
On the other hand, nitride’s ultra-hard surface excels in reducing friction, which can lead to a smoother action and potentially extend the barrel’s life by minimizing wear. This finish is also low-maintenance, as its inherent lubricity reduces the need for additional oils that can attract dirt and debris. For those who prioritize a no-fuss, long-lasting solution, nitride is often the go-to choice.
Both Cerakote and nitride finishes have their own set of advantages, and the decision between them can also be influenced by cost considerations. Cerakote, while offering a robust shield against wear and corrosion, can be more expensive due to the labor-intensive application process. Nitride treatments, in contrast, are generally more cost-effective and can be a more economical choice for large-scale applications or for those on a tighter budget.
Ultimately, the choice between Cerakote and nitride finishes will depend on the individual shooter’s needs. Whether prioritizing the customizable, high-temperature resilience of Cerakote or the sleek, low-maintenance durability of nitride, both options represent the pinnacle of modern barrel finishing technology. By selecting the appropriate finish, gun owners can ensure that their barrels are not only protected from the rigors of use but also optimized for peak performance, shot after shot.
In conclusion, the debate between Cerakote and nitride finishes is one of preference and purpose. Both coatings offer superior protection and enhanced performance, but they do so in different ways. By understanding the unique properties and benefits of each, shooters can make informed decisions that align with their specific needs, ensuring their firearms are well-equipped to handle whatever challenges come their way.
The Role of Barrel Coatings in Enhancing the Lifespan of Your Firearm
Barrel Coatings and Finishes: Enhancing Durability and Performance
The longevity and reliability of a firearm are paramount to its performance, especially under harsh conditions. One of the most critical components in ensuring a firearm’s durability is the treatment of its barrel. The role of barrel coatings and finishes cannot be overstated, as they serve as the primary line of defense against a myriad of factors that can compromise the integrity and functionality of the barrel. These coatings are designed to protect against corrosion, reduce wear, and in some cases, even improve the firearm’s accuracy.
Traditionally, gun barrels were susceptible to rust and corrosion due to the high moisture environments they were often exposed to. However, with the advent of advanced coatings, the susceptibility has been greatly reduced. One of the most popular coatings is the Parkerizing finish, a phosphate-based treatment that provides a degree of corrosion resistance and a non-reflective surface. This finish is particularly useful for military firearms that are exposed to extreme conditions and require a non-glare surface for tactical purposes.
Another innovative coating is the use of nitriding processes, such as Ferritic Nitrocarburizing (FNC) or Tenifer, which imbue the surface of the barrel with nitrogen and carbon. This process not only hardens the surface, making it more resistant to wear and tear but also provides excellent corrosion resistance. Nitriding treatments are known for their ability to maintain the precision of the bore, which is crucial for maintaining accuracy over the lifespan of the firearm.
Moreover, the application of PVD (Physical Vapor Deposition) coatings, such as Titanium Nitride (TiN), has gained popularity due to their ability to provide a hard and durable surface while also reducing friction. This reduction in friction means that there is less heat generated during firing, which contributes to a longer barrel life and potentially improved accuracy, as excessive heat can warp the barrel and affect the bullet’s trajectory.
Cerakote is another finish that has revolutionized barrel coatings. It is a ceramic-based coating that can be applied in thin layers and comes in a variety of colors. Cerakote is renowned for its high resistance to abrasion, corrosion, and chemicals. It also withstands high temperatures, making it an ideal choice for barrels that experience rapid and intense heating. The versatility of Cerakote allows for customization in appearance without sacrificing the protective qualities essential for a durable firearm.
The application of these coatings and finishes is a meticulous process that requires precision and expertise. It often involves cleaning the barrel to a bare metal state, applying the coating, and then curing it under specific conditions to ensure maximum adhesion and effectiveness. This attention to detail ensures that the coatings perform as intended, providing a long-lasting barrier against the elements and operational wear.
In conclusion, the role of barrel coatings and finishes in enhancing the lifespan of your firearm is a testament to the advancements in firearm technology. These treatments not only protect the barrel from environmental and operational hazards but also contribute to the overall performance of the firearm. By selecting the appropriate coating or finish, gun owners can ensure that their investment is protected, and their firearm remains reliable and accurate for years to come. As the industry continues to innovate, we can expect even more effective and efficient methods to emerge, further enhancing the durability and performance of firearms.